Vehicle Emissions Test
H2 Fuel Save was put through some rigorous testing by the Department of Transport Energy and Infrastructure and passed with impressive results. Testing was performed using all the same constants with the only difference being the comparison between standard diesel without the H2 system and with the H2 System
Department of Transport and Infrastructure – Emission Test Diesel only | DIPTI-Testing-Diesel-Only |
Department of Transport and Infrastructure – Emission Test Diesel and H2 | DIPTI-Testing-Diesel-and-H2 |
It is no longer a matter of will hydrogen be a part of the mainstream energy mix it is now a matter of how quickly can it be introduced to be a catalyst in the de-carbonising agenda that most governments and industries are after.
Early R&D
H2FSA completed a phase of intense R&D in the areas of suitable materials, heat dispersion, extremely fine current control, and strength of design. The final result was a device suitable for the extreme requirements of all Australian transport Industry
Safety
This one factor must be at the forefront of all design aspects , firstly as the reactors are where the H2 & O are produced their strength of construction was paramount, they were tested in a confined blast cabinet while full of H2 & O and ignited. There was some small distortion in the outer wall, no fracture to any welds or seams, and in once case the sight tube did split open.
As the H2 atom is both extremely small and also light if a leak in the supply line occurs the H2 gas will dissipate upwards at greater than 500km/hr and instantly become inert within the atmosphere.
In all of the applications both here in Australia, in Europe and in Asia there has never been an issue that resulted in the need for the safety features of the H2FSA system to activate.
H2 FSA has designed the system so as in a transport application the Hydrogen reactors remain at approximately 15 degrees above ambient temperature without the need for external fans that draw additional energy from the host vehicle and take up valuable space.
H2 FSA has tested the anode and cathode after 1 million km of use and found that there was zero hydrogen degradation. The system is designed to last at least 3 million km.
The strength and vibration tests we conducted on a Kenworth Cabover that traveled the Oodnadatta Track every second day for 6 months, not one component failed.
![]() | ![]() |
Electronics
To achieve the degree of robust build quality and current control we required, we worked with a leading Australian electronic manufacture Imark Communications in Melbourne. Imark Communications clients include SA Power Networks and the ADF. Their work in providing power supplies into the mining sector and the military plus their Solar Regulators provided the high level of design and manufacturing expertise that we required. The head of electrical engineering at Melbourne University Dr James Brown also worked in conjunction with Imark on this project, this collaboration resulted in having extremely fine amperage control +_ .2 of an amp and holding. Our systems can read 36, 24, 12 volts, has reverse polarity protection and a max operating temperature of 100 deg C.
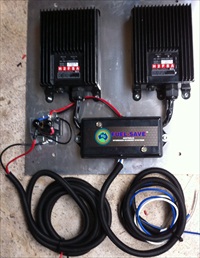
The electronic control modules are manufactured in Melbourne Victoria. This is so we can guarantee quality and also control the supply chain
The system is wired in such a way that when the engine starts there is no H2 in the motor, when the batteries charge up to a point the system then activates.
Unique Proprietary Knowledge.
Within the supplemental hydrogen field using electrolysis to create H2 & O to be introduced into the combustion chamber of Internal Combustion Engine (ICE) with the aim to reduce fuel consumption, reduce emissions and increase various performance factors of the ICE the difficulty arises of how much H2&O is the most beneficial.
At H2FSA again we followed the previous known science from Cal Tech. Remembering that a stoichiometric equivalence factor (λ = 1.00) means an air-fuel ratio of 14.7:1 for gasoline engines and 14.5:1 for diesel engines.
Working on this basis of 14.5:1 for diesel engines. it was determined that the actual engine size was of little relevance when it came to fuel burn. Example: you can have a 3lt motor doing very lite load work which would result in low fuel use, or the same motor could be under heavy load and burn three times the fuel value. Therefor supplying an amount of H2&O simply based on engine size would not give the best burn results required to achieve the parameters required on a repeatable basis.
H2FSA through extensive trials has developed a fuel burn to H2&O formular based on fuel burn regardless of engine capacity. It is also vital to introduce the oxygen component into the combustion chamber with the H2 so as not to disrupt the stoichiometric value of the burn process. Because the flame speed is now approximately 10X faster the power stroke of the engine is now also partly a cooling stroke. It is this formular that is part of our proprietary knowledge. It is because of this and other aspects of the H2FSA system that we have never caused any damage to any engine diesel or petrol in over 300,000,000 km in real world applications. On a truck pulling approximately 70 tone the power draw from the host electrical system is the equivalent of less than half of one HP back to the H2FSA system to achieve a return of 12% reduction in fuel consumption, 15% extra torque while decreasing exhaust temp by greater than 40 deg c.
